Absolute Measuring Gauge For Pre-In-Post Process on Grinders
PROTOMAR™
In order to satisfy increasing quality requirements in the production of medium and large parts, such as broaching tools, railway axles, printing rolls, milling rollers, etc., Marposs has developed the Protomar range of diameter measurement heads for use both during and after the grinding process. The main feature of Protomar is that it is an absolute measurement gauge, meaning it is capable of measuring any diameter within the measurement range it has been set-up for, without the need for specific zero-setting, but simply by calibrating it using a Master having a known value. The PROTOMAR measurement ranges were set-up based on various part types and dimensions. Accuracy and repeatability errors are kept to an absolute minimum, irrespective of whether the part section surface is continuous or interrupted.
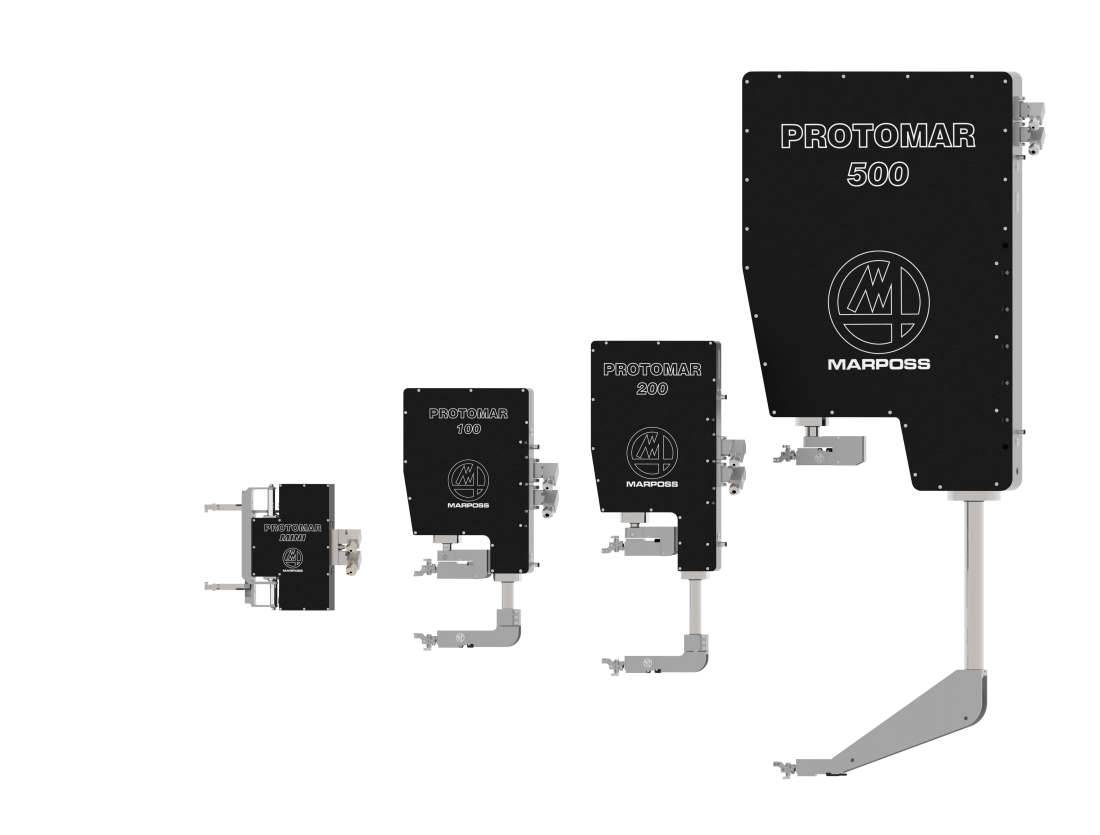
During the grinding process, the measurement uses the nominal Master value, acquired during the zero-setting procedure, as its reference value. In this way it’s not necessary to use a master part for each diameter to be ground.
The diameter measurement value is obtained combining the two values detected by the measuring cells and the position of the incremental optical transducers mounted inside the head body. Upon completing each grinding cycle, once the programmed diameter has been obtained, the system opens the contacts either in the safety position (maximum aperture), or so that the aperture is optimised for the value of the subsequent diameter.
In order to reduce cycle time, the control unit optimises the cell holder arms movement speed according to the processing phases, so that it’s at the maximum value during the opening/closing movements. During the machining process, the cell closure speed is regulated, according to the amount of stock removal detected, so that the necessary contact between the measuring contact and the part is always guaranteed. This also protects the cells against the risk of impact in the case of interrupted surfaces.
- Large measurement range
- Real time diameter measurements at every position on the part and on any type of surface
- Diametral and longitudinal part profile analysis
- No need for zero-setting for individual part types
- Ideal for processing or measuring single parts
- Flexible machine installation
- Collision control system for out-of-range parts/diameters
- Reliability, sturdy build, sealed against even the highest volumes of coolant
- Cell holder arm movement speed optimised based on the working/approach phase
- Immune to variations in coolant temperature
In order to cover the various application ranges, the Protomar absolute gauge is available in the following versions:
- Protomar 100 – Series S, typically used on multi-diameter applications for gear wheels in pump systems
- Protomar 200 – Series M, typically used on multi-diameter applications for broaching tools
- Protomar 300/500 – Series L, typically used on railway axle, wind turbine and printing roll applications
- Protomar 700 – Series XL, typically used on milling roller applications